Process Improvement and Optimisation
Based on numerous projects where Rethink has assisted clients with their Improvement and Optimisation initiatives, Rethink has developed its own approach, the TPI framework, which comprises 4 key elements for achieving optimised operations and ongoing continuous improvement:
- Business Process Improvement and Business Process Reengineering (BPR)
- Workforce Management
- Workforce Alignment
- Performance Management
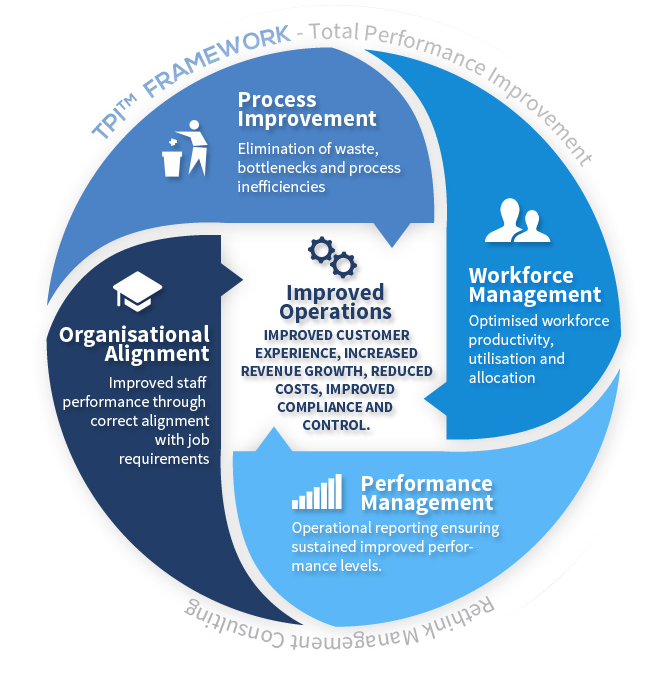
Process Improvement / Process Reengineering
This element is focused on the improvement and optimisation of business process efficiency through the elimination of waste and inefficiencies, and is delivered via Rethink’s BPR approach that is based strongly on LEAN Six Sigma and business process analysis.
Workforce Management
This element focuses on improving the performance of a process by raising workforce productivity through focused management and scheduling. The key elements of this are:
- Determining the relationship between workloads and staffing requirements
- Capacity planning - determining optimal operational staffing levels and organisational structures
- Forecasting workloads and scheduling staff accordingly
- Monitoring and management of workforce production to the set performance targets
- Manager, Supervisor, Team Leader coaching in monitoring and managing their areas to ensure the optimum balance between costs, quality and service levels.
Organisational Alignment
Critical to process performance is having the right skills for executing the required work. This element of TPI focuses on aligning workforce skills and experience with the process requirements. It involves comprehensive job analysis and design, supported by an independent assessment methodology that assesses staff competency, ability and personality.
Performance Management
This element focuses on implementing a process focused dashboard that enables management to monitor how an operation is performing in terms of the cost, quality and customer service targets of the processes. Processes that are underperforming are then addressed using the other three TPI elements, in order to bring them back on line with the set targets. Implementation of this element focuses on establishing the dashboards and embedding the processes for the continuous monitoring of process performance and taking corrective action to address any non-conformances.
The outcome of Rethink’s Operations Improvement and Optimisation assistance is reduced costs, errors and processing times, and hence improved profitability, service, quality and human resource planning.
Note: Although TPI can be undertaken as a once off initiative, it is ideally implemented as a Continuous Improvement / Continuous Process Improvement framework.